NEWS
Quayside-to-Seabed: Boosting efficiency in mooring T&I
With demand rising for floating production units, Jumbo Offshore
Business Development Manager Americas Alexandra Santiago Marino
discusses an efficient approach to mooring installation.
Floating production facilities are not likely to be going anywhere soon. As operators move into ever deeper waters for increased production, focus is on reducing CAPEX and OPEX costs for the future. As a result, we see floating production facility designs used repeatedly in order to fast track projects. Notably, this is taking place in the Americas, particularly in the GoM, Guyana and Brazil.
At the same time, operators are looking for reliable, efficient transport and installation contractors to help bring their plans to fruition. Jumbo Offshore has made the installation of floating facilities a focus market. The company has been actively streamlining the installation process of these facilities to support cost saving measures for fast-track projects. To create predictability, the company has fixed its attention on the transport and installation of mooring systems.
Efficient mooring installation
In a conventional installation, numerous assets are required. The mooring system is loaded onto a barge and towed by a tug to the installation vessel waiting offshore. With Jumbo’s Quayside-to-Seabed approach, the system is loaded onto a single, relatively small – and cost efficient – vessel such as Jumbo Offshore’s J-Class Heavy Lift Crane Vessels.
With significant vessel intake capability, high crane capacity, and high speed, more mooring system components can be transported and installed in fewer trips in comparison to traditional installation methods.
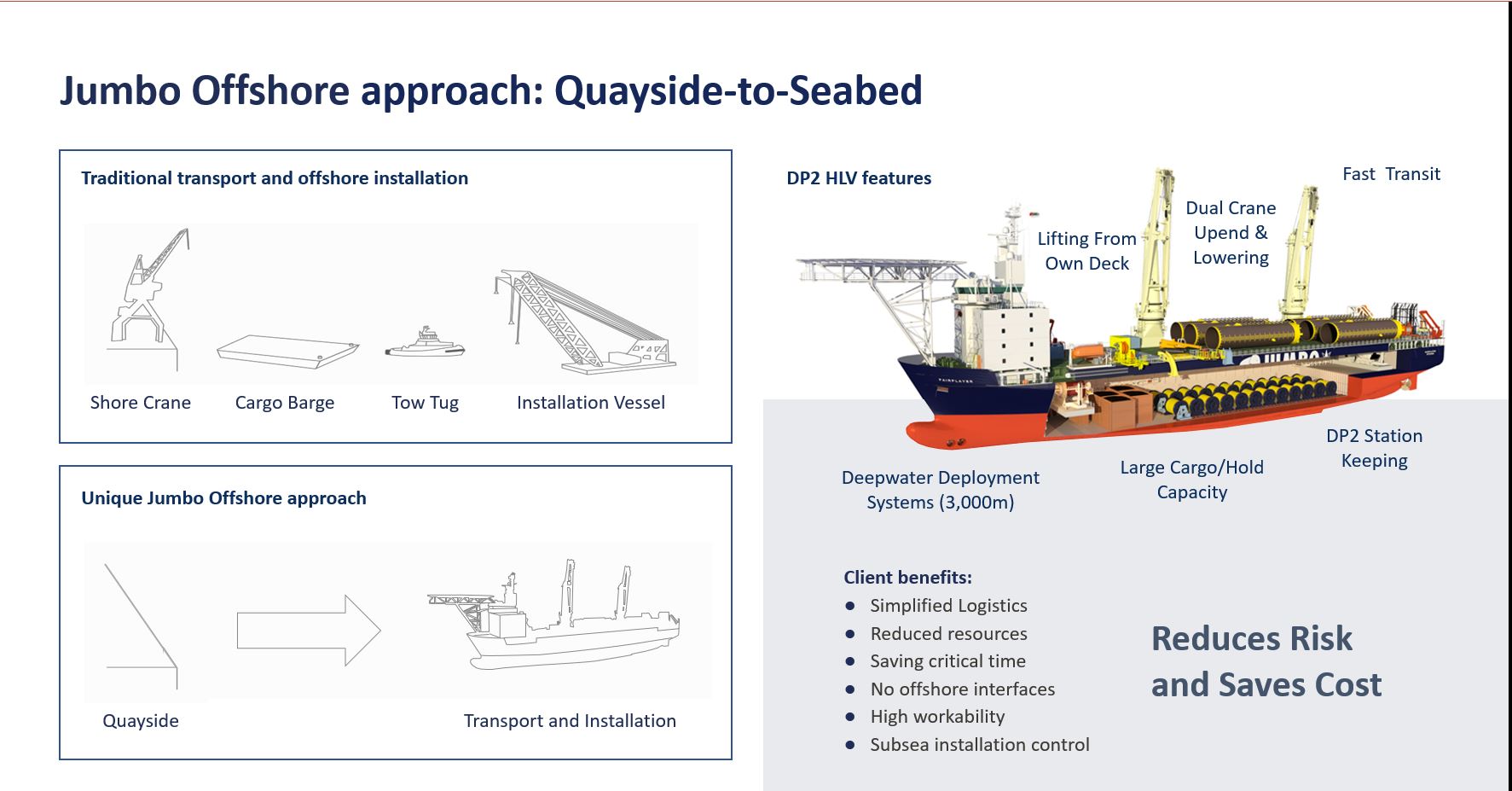
This ensures that much of the work is done well in advance of the floating unit’s arrival, with sufficient time to undertake any corrections, or resolve any challenges.
The process represents a significant simplification of the logistical process and a considerable boost for efficiency, in terms of both time and cost. Furthermore, with less assets involved, and a reduction in working hours, it also provides a route to increased safety.
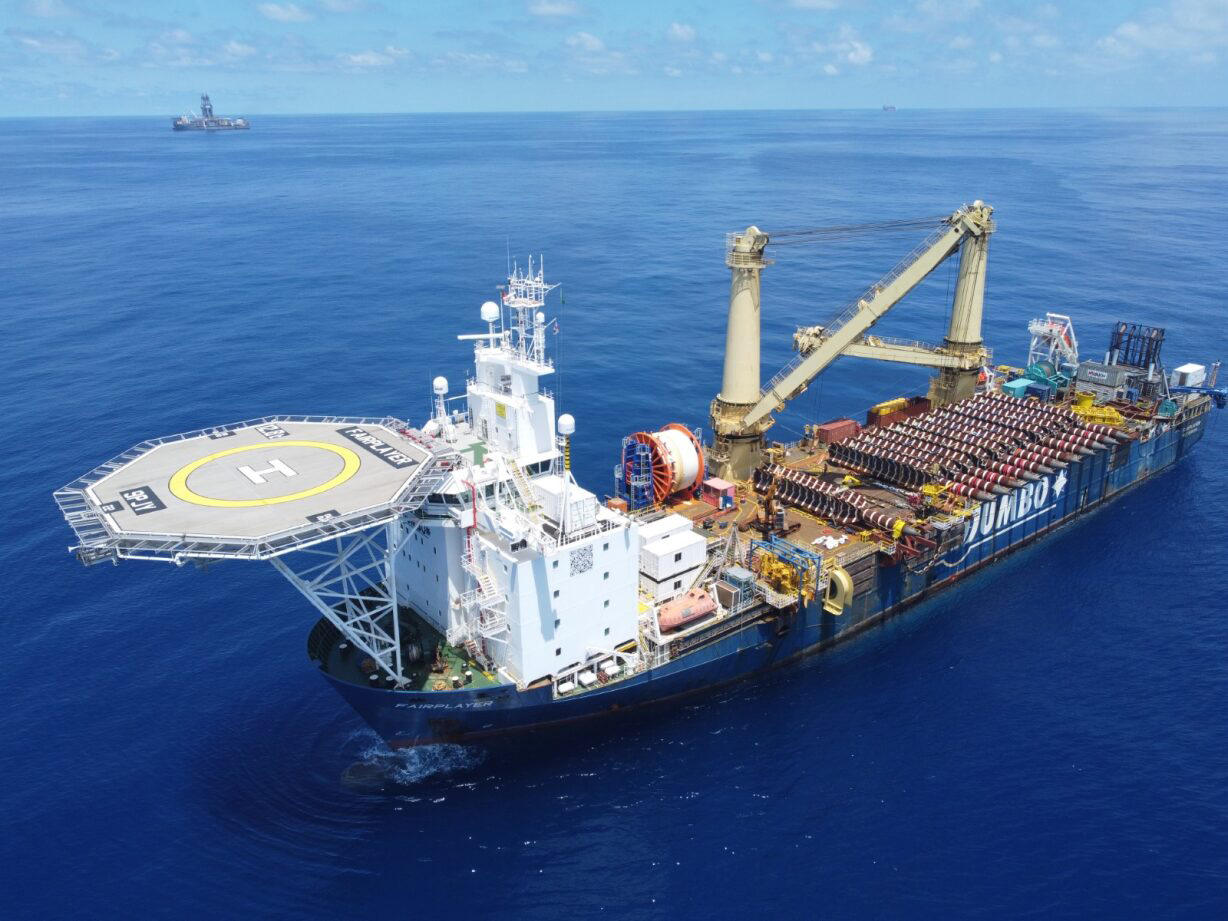
Fairplayer transporting and installing torpedo anchors
Considering CAPEX & OPEX
Besides the added efficiency involved, there is another argument in favor of Jumbo Offshore’s approach; the limited number of assets such as anchor handlers available in the market to undertake this work.
Plus, the deeper the water, the larger the mooring components become, which makes the pool of available vessels even smaller. As the designs trend toward larger components, Jumbo Offshore is able to grow with the market. The Jumbo J-Class vessels have the capability to reach depths of 3,000 meters and the subsea crane capacity required to handle large suction piles.
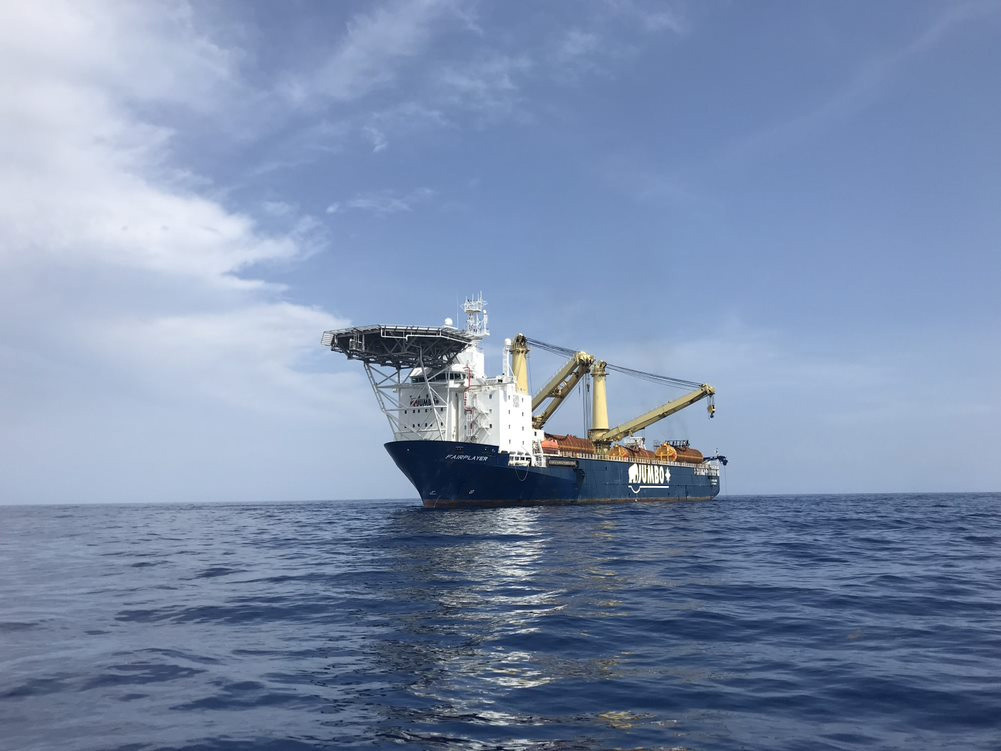
Jumbo’s HLCV Fairplayer
In particular Jumbo Offshore and its clients sees possibilities in reducing CAPEX and OPEX via off floater vessel tensioning. This is a cost-effective alternative to expansive and heavy mooring winches aboard the floating facilities. Off-vessel tensioning, such as with an inline tensioner offer a variety of benefits to operators. These include freed space on deck of the FPU with removal of mooring winches and other tensioning equipment, reduced maintenance and, ultimately, improved safety operations.
Track record
Jumbo Offshore has showcased its streamlined deep water mooring system installation technique on a number of projects. These include floating facilities in the GoM (1,250 meters), in Israel at (1,750 meters) and a production, storage and offloading facility in Brazil (2,000 meters). Presently, the company is busy preparing for an FPSO installation in Guyana (1,670 meters), which will include nineteen suction anchors and mooring lines.
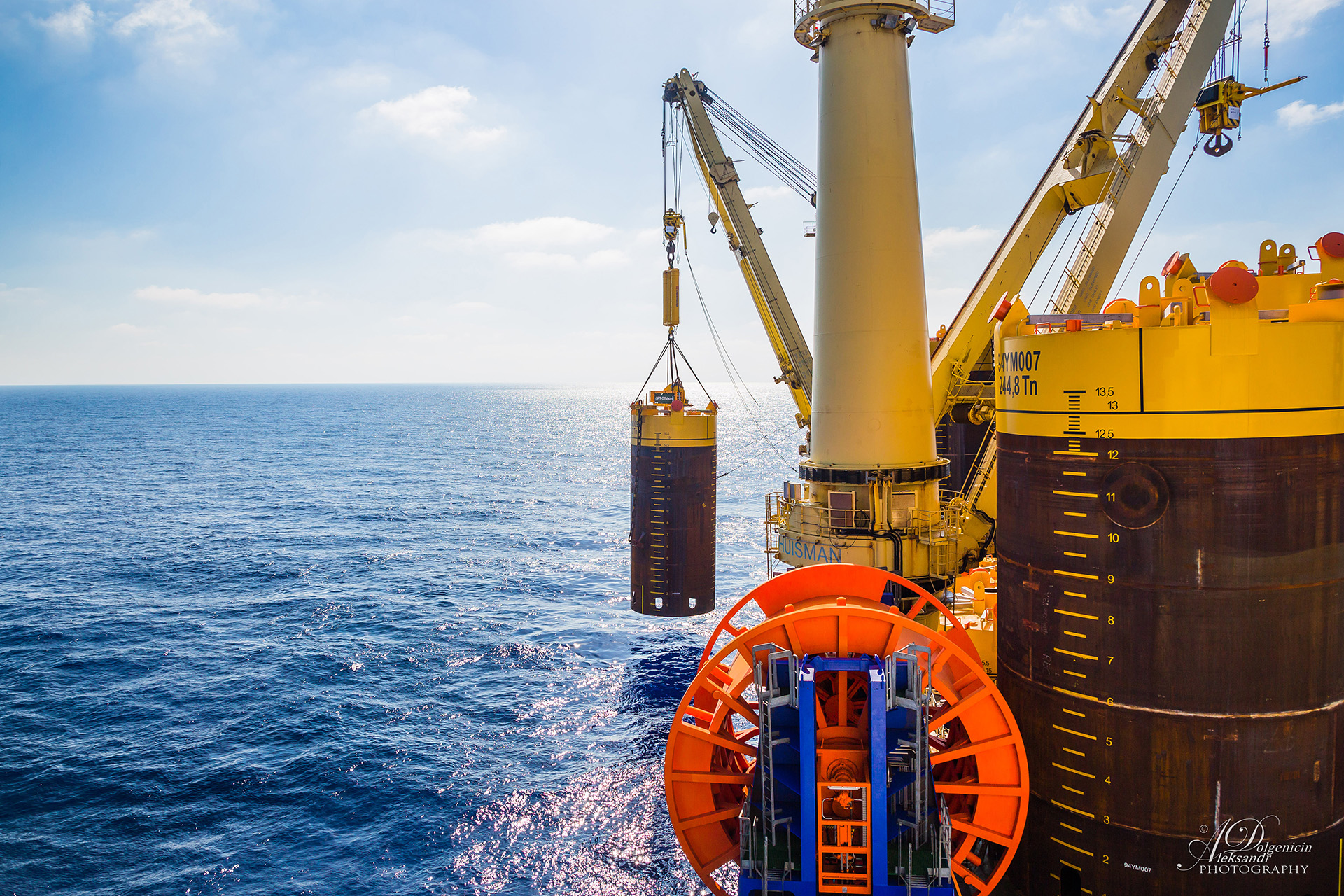
Suction piles transported and installed in the Mediterranean
With these projects under its belt, Jumbo Offshore has developed extensive expertise in installing these systems. As demand continues to grow for floating production units, in parallel with increasing cost consciousness, the company is looking forward to supporting its clients with niche solutions such as this one to enable their continued success.
Sponsored content from Jumbo Offshore
Written by Alexandra Santiago Marino
Business Development Manager Americas
jumbomaritime.nl